Busbar Coating: The What, Why, and How for Electrical Safety
In the field of electrical engineering, where invisible currents of power flow, there exists a silent hero known as the bus bar. These unassuming metal strips quietly carry the lifeblood of electricity through substations, switchgears, and control panels making sure our lights shine and our machines run smoothly.
Yet, in the face of moisture, corrosion, and the relentless march of time, even the mightiest of bus bars can find themselves in need of protection—a guardian to shield them from these threats and potential disasters. That’s where bus bar coating comes into play.
It’s an unsung hero in electrical systems, providing both insulation and defense against rust. This ensures our electrical infrastructure remains strong, reliable, and always ready to power our modern world.
In this article, we’ll uncover the secrets of bus bar coating. We’ll explore how it works, the science behind it, and why it’s crucial for keeping our daily lives electrified. Join us on this enlightening journey into the world of bus bar coating, where science, engineering, and electricity come together to safeguard the sparks that brighten our modern existence.
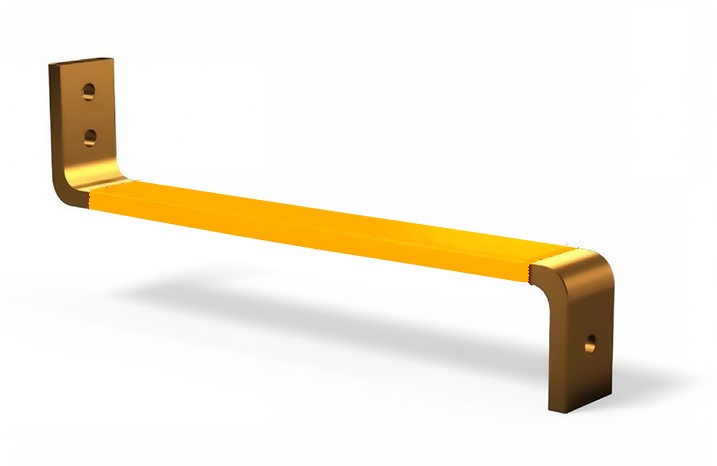
Why Busbar Coating
Bus bar coating is employed for several important reasons in electrical systems:
1. Electrical Insulation
One of the primary reasons for bus bar coating is to provide electrical insulation. Bus bars carry high-voltage electrical currents, and without proper insulation, there's a risk of short circuits or electrical faults. Coating the bus bars with insulating materials ensures that they don't come into contact with other conductive components, preventing unintended electrical connections.
2. Corrosion Protection
Bus bars are typically made of metals like copper or aluminum, which can corrode over time when exposed to moisture, chemicals, or environmental factors. Coating the bus bars acts as a barrier, protecting them from corrosion and extending their lifespan.
3. Environmental Protection
Bus bars are often located in environments with harsh conditions, such as industrial settings or outdoor installations. Coatings provide a protective shield against these conditions, safeguarding the bus bars from damage due to exposure.
4. Safety
Coating the bus bars enhances safety by reducing the risk of electrical accidents. It helps prevent accidental contact with live conductors, reducing the potential for electric shocks or fires.
5. Enhanced Efficiency
By preventing corrosion and minimizing electrical faults, bus bar coatings contribute to the efficient and reliable operation of electrical systems. This, in turn, reduces downtime and maintenance costs.
6. Compliance with Standards
In many industries, there are specific standards and regulations that require the use of bus bar coatings to ensure safety and reliability in electrical installations.
How Busbar coating works
Bus bar coating functions by enveloping the bus bars, which are metallic conductive strips in
electrical systems, with a protective layer. This protective layer serves a dual purpose: electrical
insulation and corrosion prevention.
1. Electrical Insulation
Material Application:
Specially designed insulating materials, such as epoxy resins, silicone, or polyurethane, are applied onto the surface of the bus bars. These materials have properties that prevent the flow of electricity.
Barrier Creation:
Once applied, the insulating coating forms a seamless and uniform barrier around the bus bars. This barrier effectively isolates the conductive metal from its surroundings, blocking direct electrical contact.
Short Circuit Prevention:
By creating this insulating layer, bus bar coating minimizes the risk of electrical shorts or malfunctions, as it prevents unintended electrical connections between the bus bars and
other components.
2. Corrosion Protection
Barrier Formation:
Bus bar coatings establish a protective shield that shields the underlying metal from
environmental elements, including moisture, chemicals, and contaminants.
Corrosion Resistance:
This shield hinders the penetration of moisture and corrosive substances, effectively
preventing oxidation and corrosion of the bus bars. By doing so, it maintains the
structural integrity of the bus bars and extends their operational lifespan.
In essence, bus bar coating acts as a safeguarding envelope for bus bars, ensuring their secure
and dependable operation within electrical systems. It achieves this by offering electrical
insulation to reduce the risk of electrical issues and corrosion protection to shield against
environmental damage, thereby enhancing equipment longevity and reliability.
Now, you might be wondering who can provide this essential service with expertise and
reliability. With a remarkable 40-year experience in the electrical industry, there is a company
you can trust – Sundial.
Sundial’s extensive experience and commitment to excellence make it the perfect partner for
your electrical needs. With Sundial, you can rest assured that your electrical infrastructure will
receive the utmost care and protection.
So, if you are looking to secure the longevity and reliability of your electrical systems, consider
Sundial. With our proven track record and dedication to innovation, together, we can ensure that
the sparks of progress continue to light up our modern world.
Ready to safeguard your electrical future? Contact Sundial today and embark on this journey of protection and innovation. Do not hesitate; Contact Us now!